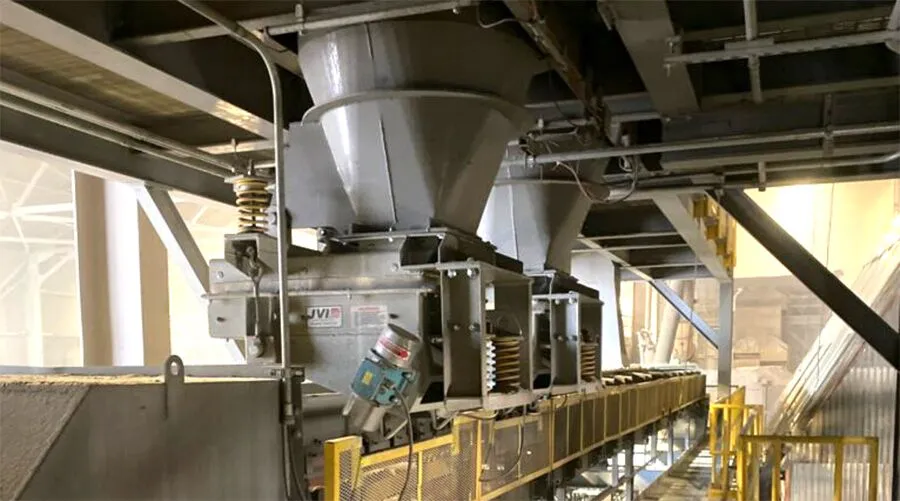
Alloy Handling Systems for Steel Mills
Alloy handling systems are an integral part of steel mills. These systems are used for receiving, storing, transporting, and batching materials. To support our steel mill customers, Wm. Neundorfer & Co. partners with Conveyors Etc., Inc. They are professionals with over 75 years of experience in the design and supply of alloy handling systems. In this article we will cover what an alloy handling system is, their key components and functions, and the benefits they provide.
Alloy Handling System
An alloy handling system in a steel mill is a critical component designed to manage the movement, storage, and precise addition of various alloying elements into the steel during the production process. Alloys are added to steel to improve its properties, such as strength, corrosion resistance, and hardness, and the handling system ensures that these materials are accurately dosed, transported, and mixed into the molten steel.
Key Components and Functions of an Alloy Handling System:
Conveyors Etc., Inc alloy storage bins.
Storage of Alloy Materials:
The system stores different alloying elements, such as carbon, manganese, chromium, nickel, vanadium, and others, in controlled conditions to ensure their quality is maintained before use. These alloys may be stored in silos, bins, or hoppers, depending on the type and form of the material (e.g., powder, ingot, or granules).
Transportation:
Alloy materials are typically transported from storage to the point of use using various methods such as conveyors, screw feeders, pneumatic conveying systems, or even cranes. The transportation system ensures that alloys are moved efficiently and safely throughout the mill.
Batching and Dosing:
Accurate dosing and blending of alloys are essential to produce the desired steel composition. The alloy handling system often includes automated batching and weighing equipment that ensures precise amounts of each alloy are added to the molten steel at the right time during the steelmaking process.
Injection into the Furnace:
Once the correct quantities are determined, the alloy materials are injected into the molten steel through various mechanisms such as injection lances, feeders, or drop-bottom systems. The alloying elements are typically added into the electric arc furnace (EAF), blast furnace, or ladle refining furnace, depending on the stage of production.
Monitoring and Control:
Modern alloy handling systems incorporate sensors, load cells, and automation for real-time monitoring and control. This ensures the right amount of alloy is added and that the steel chemistry is kept within specifications. The system is often integrated with the steel mill’s process control system for seamless operation.
Safety and Environmental Management:
The handling system also includes safety features to protect workers from hazardous materials and conditions. Additionally, it helps in controlling emissions and ensuring that any dust or fumes generated during the handling and transport of alloys are managed appropriately through filtration and containment systems.
Advantages of an Alloy Handling System:
- Precision: Ensures accurate amounts of alloy are added, leading to consistent steel quality.
- Efficiency: Automates many tasks, reducing manual labor and improving throughput.
- Flexibility: Can handle a variety of alloying materials and adjust to changing production requirements.
- Cost-Effectiveness: By improving material usage and reducing waste, the system can help lower overall costs.
- Safety: Enhances worker safety by minimizing direct exposure to potentially hazardous alloys.
Applications:
Alloy handling systems are used in various stages of steelmaking, including the production of different steel grades such as carbon steel, stainless steel, and high-strength alloys. The systems are essential for maintaining consistent material properties required for applications like automotive manufacturing, construction, and heavy machinery.
For more information or details on how we can help you select the right equipment for your application, contact Wm Neundorfer & Co today.
We have the expertise and experience to ensure you get the advice and recommendations you require for your specific application.