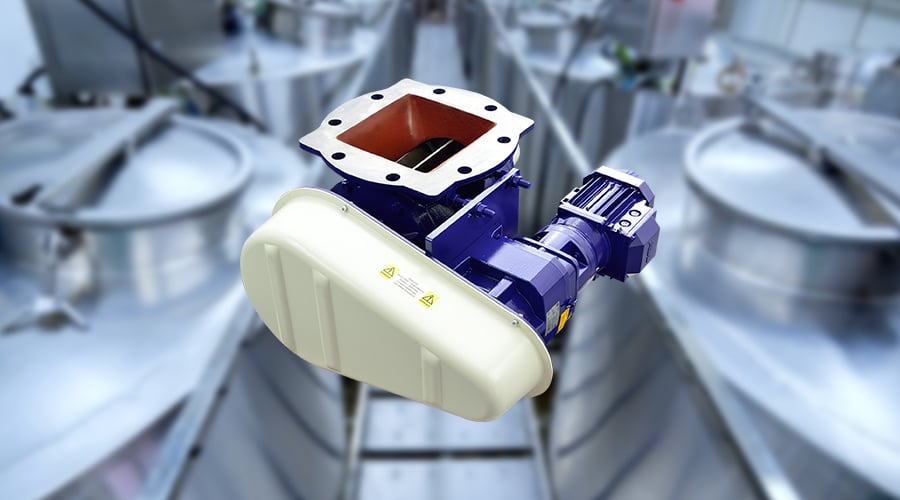
Rotary Airlock Valves: Features, Characteristics and Considerations
Rotary airlock valves can be found in use across a broad expanse of industries. They are commonly found in the food and beverage industry, chemical and petrochemical industries, plastics industry and agricultural industry where the need to maintain an airlock between two pieces of process equipment is fairly common. Additionally, the rotary valve can also be found in the aggregate industry, asphalt industry, bio-mass industry, cement, power and even foundry industries where users find a need to regulate material flow within their processes. In some instances, the dual functionality of the valves allows them to perform multiple roles within the process stream. This seemingly simple, ruggedly dependable, and very diverse piece of process equipment lends itself nicely to a wide range of applications throughout a multiple field of industries.
In this article, we will look at some of the features and characteristics of rotary valves and see how these features allow them to fit into the process stream.
A rotary valve is a fairly simple piece of equipment that is utilized to maintain pressure differential between an inlet and an outlet or as a means to control material flow rate as required. In some instances, the valve may serve both purposes. In either case, what is being accomplished is that material is being moved from the inlet of the valve to the outlet. An important aspect in overall valve functionality is the characteristics of the material being handled. Rotary valves perform best when moving dry, free flowing products. However, in many situations, dry, free flowing products are not necessarily the products that are found passing through the valve. As a means to overcome the difficult conveying characteristics of some of these more aggressive materials, there are some added features which can be incorporated into a rotary valve to aid its performance when required.
In instances where the material being handled could have a possibility to stick, pack, or build up within the pockets of the rotary valve, there are a few options to be considered to help overcome the product’s inherent nature to build up in the valve pockets. The first of these would be to coat the valve rotors with a non-stick coating such as a PTFE lining to help prevent material adhering to the valve pockets as it is presented during the fill cycle. Another option would be to utilize a concave rotor arrangement which allows materials to move more freely from the valve pockets during discharge. This feature allows product to drop more easily out of the pocket than it would from a traditional V-shaped valve pocket where materials have a tendency to stick, adhere, or pack more freely into the pocket channels. Lastly, and if the rotor arrangement permits, it would be possible to utilize an air stream to help force material from the rotor by incorporating a drilled and tapped end cover purge port. This would allow a stream of air into the valve to help dislodge any material packed into the pockets.
In many process streams, rotary valves are found handling a wide variety of products that are of larger sizes and have a tendency to jam or bind the valve during operation. This is most common with non-friable materials that do not break apart easily and tend to get trapped between the valve body and blades. To help reduce the possibility of this occurring with standard rotary valves, the incorporation of either inlet baffle meters or inlet shear plates could help decrease product shear as well as reduce the possibility of material contact between the rotor blades and leading edge of the valve inlet where jams and binds tend to occur. If space is limited and inlet shear plates or baffle meters are not feasible, then the use of an offset rotary valve could be considered. An offset rotary valve incorporates a rotor that is “offset” from the inlet. What this does is allow the valve to constantly fill with material as the rotor moves upward. This in turn reduces the amount of material in each valve pocket and allows material to drop into the following pocket as it rolls into position on the upswing. In this arrangement, there is less shearing action, which reduces the possibility of material jams or binds between the valve’s leading edges and the valve inlets.
Many materials presented to the rotary valve will be abrasive and have significant wear effects on both the valve’s body and blades. In addition to causing physical wear, the effects of abrasive materials also increase the already tight tolerances between the blades and body of the valve. This will have a severe impact on the performance of the valve in terms of leakage in a vacuum or pressure, and additionally it will impact overall performance when regulating flow in other process environments. To combat wear in abrasive environments, consideration should be given to utilizing wear-resistant materials such as tungsten carbide or hard chrome when selecting valve construction materials. Wear components such as rotor tips or rotors can be fitted with AR400 steel to aid in resisting the effects of severely abrasive materials in which they may come into contact. Lastly, a valve capable of adjusting internal rotor tolerances by means of an external adjustment (tapered adjustable rotor) is another means to help fight the effects of abrasion.
Process temperatures, and in many instances, material temperatures as well, need to be taken into consideration when looking at the performance and reliability of the rotary valve. Operational tolerances between the valve body and the blades are very tight, and increasing temperatures imposed by the process environment and/or material temperatures can impact these tolerances. If the tolerances are not set properly, thermal expansion will cause the valve to bind, jam and seize. Setting tolerances is a procedure initially performed at the factory, but it can be accomplished on site. A valve with an external adjusting type tapered rotor is an option to help reduce the possibility of running into issues with thermal expansion problems as it allows for adjustability of the rotor and body clearances as needed due to any material or process temperature changes that may occur in the operating environment.
As mentioned, these are just a few considerations and characteristics to consider when sizing a rotary valve for a process application. From process temperatures to non-stick linings, there are many factors and features that will affect the performance of the rotary valve in a given environment. Not every valve will require all of these options, and some may need more, but properly sizing the valve to the operational environment is important to its longevity, efficiency and overall performance.
For more information or details on how we can help you select the right equipment for your application, contact Wm Neundorfer & Co today.
We have the expertise and experience to ensure you get the advice and recommendations you require for your specific application.