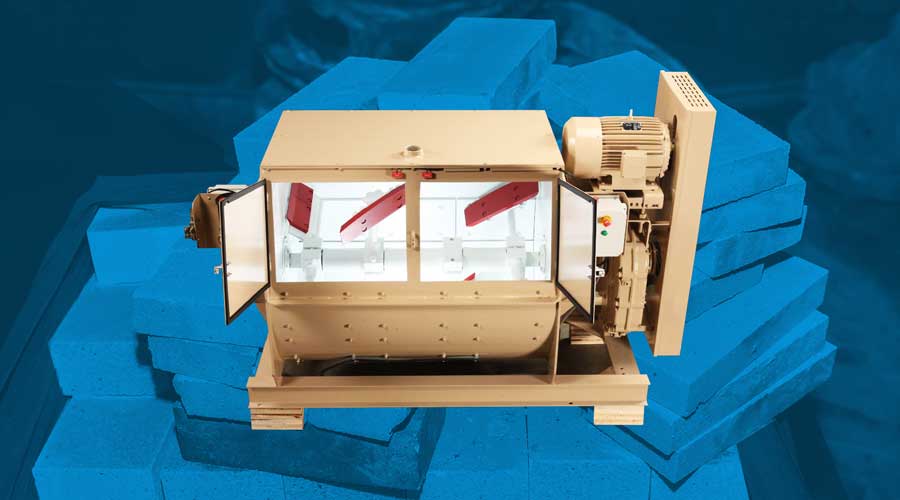
Five Must-Have Features of Refractory Mixers
Ensuring the correct mixture of a refractory compound can mean the difference between a high-quality end product and an inferior one. This is why choosing the correct refractory mixer is critical. If the mixer cannot produce high quality product while keeping up with the demands of your process, then it can become a production liability. Wm. Neundorfer & Co. has been helping our customers improve their industrial processes for over 50 years. In this article, we will discuss five features to look for in a refractory mixer to help ensure quality refractory products and improve operational safety.
Refractory Mixer Features to Look For:
Easy to use access doors
Easy to use access doors allow for quick and efficient inspection and cleaning of the mixer during routine maintenance and regular wash down periods. Look for a large discharge door that will allow for fast and clean discharge of product from the mixer following the mix cycle to keep production flowing. It will also aid in efficient cleaning of the mixer during wash down, increasing the mixer’s service life.
Integrated bagger cutter / bag breaker
The integrated bagger cutter / bag breaker aids operator efficiency and safety by eliminating the need to cut or tear open individual bags during the mixer filling process. Efficiency is increased by reducing the mixer’s fill time while safety is increased by removing the need to cut open bags. This results in more mixed batches per hour and a lower risk of operator injury.
Automatic Shaft Seal lubricators
Automatic Shaft Seal lubricators reduce maintenance hours dedicated to mixer preventative maintenance and help extend the life of the mixer’s primary mixing shaft. It ensures that adequate lubrication is provided to the mixing shaft as needed enabling the mixer to operate safely and efficiently throughout its service life.
Quick clean discharge door
The quick clean discharge door ensures rapid and thorough discharge of batch material from the mixer following the mixing cycle while providing positive closing of the mixing chamber during the mixing cycle.
The right mixer blades
Mixer blades ensure fast, thorough, and efficient mixing of material once in the mixing chamber and come in two different styles, Paddle and Spiral. The mixture material and the desired final product determine which of the blade styles is needed. Paddle Mixing Blades provide a cross current, shearing action that forces the material into itself for a more homogeneous mix. The Spiral Mixing Blades offer a lift and fold mixing action that moves the material from one side of the mixer to the other, providing a quick, thorough mixing action.
Refractory mixers are a crucial part in the manufacturing of refractory for a wide range of industries and applications. Looking for these five features in your next refractory mixer will help ensure you will produce high-quality refractory products and help improve operational safety. If you are in the market for a refractory mixer, contact WM. Neundorfer & Co. today. We have the expertise and experience to ensure you get the correct mixing and dust conditioning products for your specific application.
For more information or details on how we can help you select the right equipment for your application, contact Wm Neundorfer & Co today.
We have the expertise and experience to ensure you get the advice and recommendations you require for your specific application.