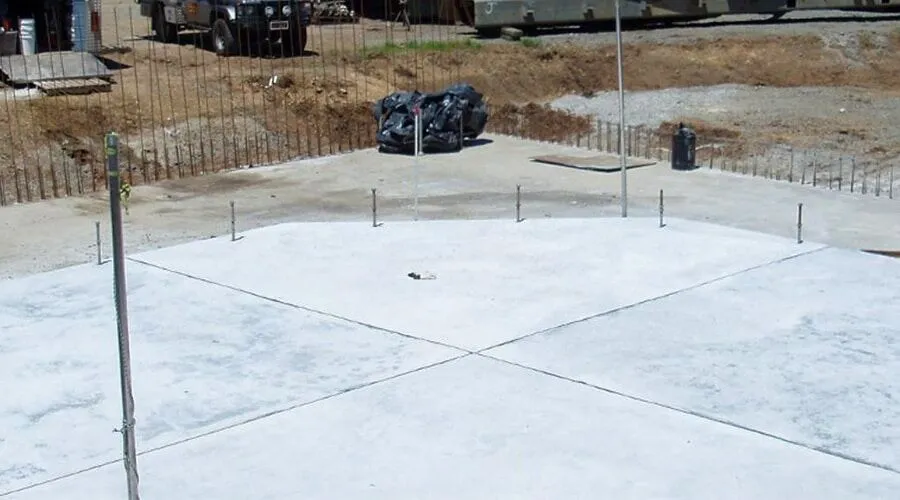
What Are Polymer Concretes and Three Types to Know
Polymer concretes can be found in many industrial structures such as pump pads, trenches, chimney foundations, process floors, and more. They provide the durability of concrete with an added chemical resistance that makes them corrosion resistant while still providing a long service life. William Neundorfer & Co. has been providing our customers with the correct information and concretes for their projects for 20 years. In this article William Neundorfer & Co. will breakdown what polymer concretes are, the benefits they provide and three types (formulations) of polymer concretes to know about.
What is a Polymer Concrete?
Polymer concrete is a type of concrete that utilizes an organic polymer to serve as the binding agent. The American Concrete Institute further defines it as:
“Polymer concrete is a composite material in which the aggregate is bound together in a matrix with a polymer binder. The composites do not contain a hydrated cement phase, although Portland cement can be used as an aggregate or filler. Polymer concrete composites possess a unique combination of properties dependent on the formulation. These include rapid curing at ambient temperatures from –18 to +40°C (0 to 104°F); high tensile, flexural, and compressive strengths; good adhesion to most surfaces; good long-term durability with respect to cycles of freezing and thawing; low permeability to water and aggressive solutions; good chemical resistance; and light weight.”
Benefits Over Traditional Concretes
Polymer concrete offers five times the physical strength of standard Portland-based concrete while also adding chemical resistance to the entire matrix. It is a monolithic providing effective corrosion protection without being vulnerable to physical abuse and a long operational life. Three major benefits of polymer concretes include:
Easy Installation
Standard mortar mixers and tools are used for mixing and placing polymer concrete. It also is applied like a traditional concrete so no new tools or training is required. Typical reinforcement is incorporated where appropriate. Minimal finishing is required. The workability of polymer concrete makes it a good choice for the construction of sumps, trenches, floors, walls and structural supports.
Short Cure Times
Polymer concretes are set by a catalyzed reaction instead of having to hydrate and then be top coated. The catalyzed reaction allows for shorter cure times and allowing the area to be put into production sooner than a traditional concrete.
Chemical Resistance
Unlike traditional concrete, polymer concretes are able to service a wide variety of environments that deal with various types of chemicals. From sulfuric acid to caustic solutions, there is a polymer designed to withstand it.
Three Types to Know
Epoxies
Epoxies offer low permeability and broad chemical resistance.
-
- Epoxy Polymer Concrete No. 165 – A general purpose epoxy with excellent physical properties.
- Epoxy NovolaK Polymer Concrete No. 265 – Popular for foundation construction, a novolac resin makes this our best epoxy for exceptional physical strength and resistance to a wide range of chemicals.
Vinyl Esters
Vinyl esters offer an upgrade to epoxy resins, particularly in the presence of bleaches and oxidizing solutions. Vinyl esters are often selected when specific chemicals exist and higher temperature resistance is required.
-
- Vinyl Ester Polymer Concrete No. 410 – This economical vinyl ester provides additional resistance to heat and chemicals.
- NovolaK Vinyl Ester Polymer Concrete No. 465 – An impermeable, fast-setting concrete offering superior heat and chemical resistance among organic materials.
Silicates
Silicates provide the optimum acidproof concrete for castable applications.
-
- Acidproof Concrete – Structural Grade No. 54SG – A modified castable material that can withstand the highest temperature ranges and acid concentrations.
With easy installation and short cure times polymer concretes offer a stronger chemical resistant alternative to traditional concretes for environments that call for chemical resistance. If you think a polymer concrete could be a solution for your application or you have a more questions about them, contact us today. WNC has the expertise and experience to supply you with the right corrosion-resistant products for your application.
For more information or details on how we can help you select the right equipment for your application, contact Wm Neundorfer & Co today.
We have the expertise and experience to ensure you get the advice and recommendations you require for your specific application.