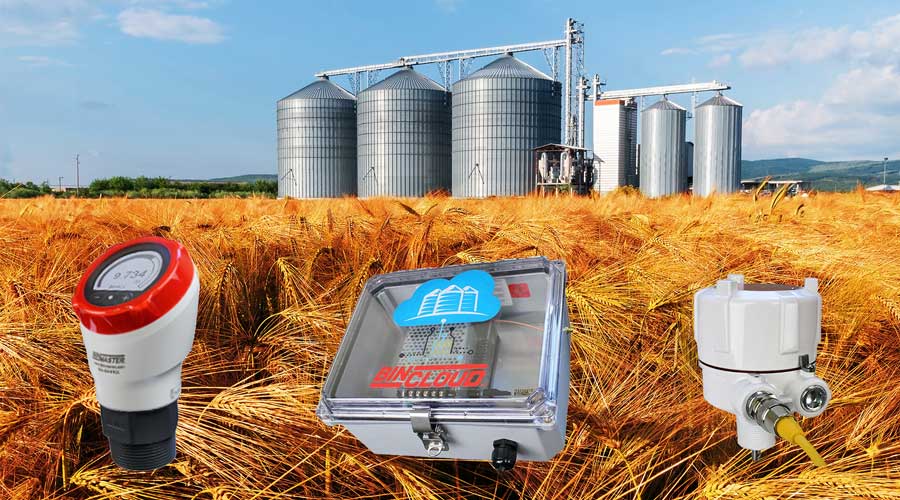
Three Things to Consider for Your Next Silo Inventory System
Real-Time Data Sensors for Industrial Environments
In today’s world, the need for accurate, real-time data has become a necessity especially in industrial environments that handle and store bulk materials in Silos. Having an accurate count of the amount of material and where it is being stored is critical to ensuring processes keep running and production does not come to a halt. To support this need for information, level sensor manufacturers have been developing new and innovative products and software for remote bin level management.
Having worked with our customers to implement these new silo inventory systems Wm. Neundorfer & Co. has found there are three things to consider when investing in a silo inventory system. In this article we will review these three items and why you should consider them.
Wireless Sensors
Running long spans of wire outdoors is often impractical. The cost of installing hundreds to thousands of feet of wire quickly becomes cost prohibitive and it is high cost of wiring that prevents an operation from becoming a more modern connected facility. Not having a connected facility with the ability to monitor silos, bin, and vessels causes personnel to be disconnected from their inventory. The solution to this? Wireless Sensors. These devices were the missing link between sensors and the software that could provide workers with the data to do their jobs better. Wireless bridges and gateways have become reliable in getting data from point A to point B and are now robust and durable for even harsh outdoor environments. At the same time, the price of these devices has come down significantly—making a connected plant affordable. They also reduce installation costs to just a fraction of the cost of hard wiring.
Mobile Access to Data
The explosion in growth of mobile devices over the last decade has brought with it a new expectation in the access to information. More and more employees are expecting to be able to access their inventory data while on the move. To address this inventory software that is user-friendly and optimized for viewing on mobile devices is a must. This allows any phone with internet access to become a powerful business management tool. Personnel can now access their silo inventory data from their phone whether they are at the plant or offsite.
Quick Disconnects
Industrial plants are tough on level sensors. Many are characterized by dusty, dirty, or harsh environments. This dictates that equipment is maintained on a regular basis and occasionally replaced altogether. But when you couple a lack of staff and a rigorous preventive maintenance schedule, you need a solution to make the task go quickly with less qualified staff. Adding a Quick Disconnect— or QD for short—has become a real time saver. These inexpensive accessories can take the tedious task of hard wiring sensors and turn it into a literal plug-in operation. No licensed electrician needed! Staff spend less time installing, replacing, or maintaining a sensor.
By incorporating these three things into your silo inventory system you can update your system at a reduced cost, make quicker informed decisions about inventory, and ensure maintenance issues won’t hinder productivity.
If you are looking to implement a new silo inventory project at your facility or upgrade your existing system, contact Wm Neundorfer & Co today. We have the expertise and experience to ensure you get the right inventory system equipment for your application.
For more information or details on how we can help you select the right equipment for your application, contact Wm Neundorfer & Co today.
We have the expertise and experience to ensure you get the advice and recommendations you require for your specific application.